Gather and leverage your business’s data to evolve your operations. No matter the size of the project or the complexity of workflows, we help you make sense of these insights. Our innovative Operational Automation platform will save you money, enhance safety and enable you to meet compliance obligations on every project.
Tailored AI solutions for construction
Improve plant and site management with AI-powered insights
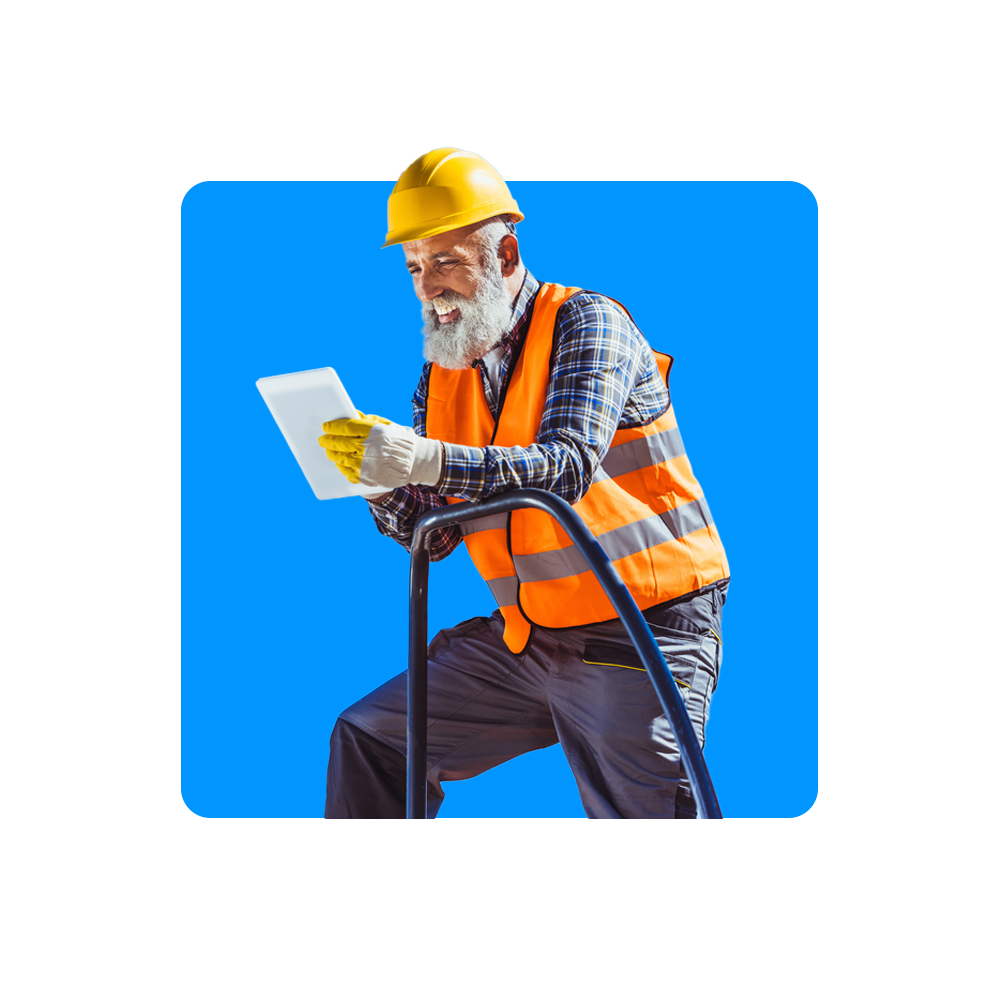
Supporting your project, whatever its needs
Every construction business and project has unique needs. At Inauro, we take the time to tailor a solution for your operations.
I need oversight of my vehicles, plant and site
Need better oversight of your plant and equipment? What about other aspects of your site? At Inauro, we help you integrate and optimise IoT devices’ real-time data analytics to provide comprehensive insights. Monitor the location, condition and use of your assets and equipment. This allows for more efficient scheduling, reduced downtime and improved resource allocation.
I need more insights on how my assets function
Ready to delve deeper into each asset’s specific needs? Through detailed data collection, we provide tailored, actionable insights. This approach enables you to identify potential issues during pre-starts, streamline induction processes, and optimise servicing schedules. By doing so, you can extend asset lifespans, improve equipment reliability and ultimately enhance the overall productivity of your construction projects.
I need to automate my processes
Time to achieve peak operational efficiency? By continuously monitoring and analysing data we’re able to help you reconcile labour costs with machine hours. Automate processes such as refuelling and simplify site induction. Our platform provides real-time insights and automated recommendations, enabling better decision-making and streamlined workflows.
We make the data work for you, which leads to:
Increased efficiency
With on-demand plant and asset management insights, you can better utilise your construction equipment. Real-time visibility into available assets not only reduces equipment costs and delivery waiting times but also helps lower labour costs by minimising idle time and ensuring resources are used more efficiently.
01
More sustainable sites
With instant monitoring and alerts, you can respond faster and more effectively to reduce fuel consumption. Alerts that reveal potential hazards, spills and breaks lead to more efficient handling and let you keep your sites cleaner and more environmentally responsible.
02
Better safety outcomes
Moving away from manual, paper-based processes to automated workflows ensures your personnel and asset management is more efficient, and reduces on-site risk. This means safer sites, which keep your teams happy, healthy and on-task.
03
Improved compliance
Using IoT solutions to continuously monitor site conditions, equipment usage and safety protocols ensures all activities meet regulatory standards. Real-time data collection and reporting facilitate timely audits and inspections, reducing the risk of non-compliance penalties.
04
Freeing up staff time
Our solutions reduce the manual workload associated with tracking equipment, monitoring site conditions and scheduling maintenance, freeing up valuable time for your team. This enables them to concentrate on strategic planning, project management and other tasks that drive business growth.
05
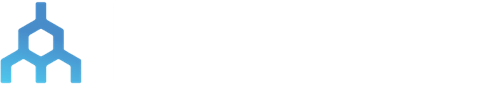
Our construction workflow management relies on our Operational Automation platform Perspio™, connects assets, telematic devices and systems to improve workflows. Increase security and safety, manage risks, ensure asset recovery, optimise waste management and reduce vehicle and asset downtime.
Track
Access real-time data from IoT devices to track equipment usage, location and performance.
Monitor
Monitor site conditions like temperature, humidity and air quality, as well as asset use to ensure safety and compliance
Integrate
Integrate data from multiple sources to optimise workflows, create efficiencies and reduce administrative burden.
Report
Perspio™ gives you complete oversight and visibility to provide clear, detailed data and reporting to clients and regulators.
Want to improve your construction workflows?
Frequently asked questions
How can I get in touch with Inauro?
Head over to our Contact page. We’ll reply as soon as we can to discuss your projects, workflows and assets, and how we can help them evolve digitally.
What construction management workflows can Inauro help us with?
We can help you to enhance visibility across your entire construction operation. Just some of the construction management workflows and processes we can help with are:
● Refuelling
● Vehicle downtime management
● Subcontractor hours reconciliation
● Fuel tax credits
● Waste management
● Plant hire optimisation
● Asset recovery
● Safety and compliance management
● Security
● Risk management
● Safety alerts
I’ve never used IoT in construction management before. Where do I start?
Using IoT in building construction doesn’t have to be complicated. At Inauro, we help construction companies identify their goals, assess their needs and choose the right IoT devices. We’ll help you integrate your software with our platform and monitor outcomes to address issues.
How can IoT make my construction workflows more efficient?
Integrating all your site data and feeding it into your enterprise applications in real time means your team can make more informed decisions.
Plus, with smart reporting, you can present contextual insights to specific team members, helping them work more effectively. By mapping out and automating your construction workflows, you can move from time-cycle-based project schedules to on-demand schedules. This lowers your costs, cuts your downtime and minimises unnecessary site activities.