Your equipment’s safety, efficiency and performance all hinge on effective plant maintenance. Whether it’s generators, excavators, fixed assets such as chillers, refrigeration units or HVAC (heating, ventilation and air conditioning) systems, telemetry is a game-changer in predictive maintenance.
Telemetry offers a more innovative way to maintain machinery by harnessing real-time data and advanced analytics. With telemetry in place, maintenance shifts from reactive—often expensive—fixes to a more proactive approach.
“A telematics device streamlines the process of maintenance management,” explains Angus Kennard, Inauro Co-CEO & Co-Founder. “The technology can be used to cut down on unnecessary maintenance and also helps with troubleshooting and planning maintenance schedules.”
The result? Significant cost savings, improved productivity and a longer equipment lifespan.
We explore how telemetry can transform plant maintenance, making it more efficient, predictive and cost-effective than ever before.
Telematics in plant service management
Plant maintenance involves a comprehensive approach that helps companies ensure their equipment and assets operate with maximum efficiency, safety, and reliability. It’s critical for operational productivity and cost efficiency and involves regular servicing, routine inspections and repairs, and other preventative measures such as condition monitoring and software updates.
While this is traditionally a manual, time-consuming task, using telemetry can change this. IoT technology allows you to use sensors on machinery and equipment to monitor parameters such as temperature, vibration and operational cycles. These sensors can provide direct data, like machine status updates, and indirect data, which can infer underlying issues.
Angus recalls the case of the catering freezers at a major stadium in Sydney.
“When we first installed the monitoring equipment, you could see that one of the freezers was defrosting every two hours,” he explains. “That process is only supposed to happen every eight hours. They couldn’t understand why the freezer temperatures were out of whack, affecting the product (in this case, gelato), but the insight from the telematics data gave them an instant answer.”
Indirect sensing can also detect anomalies in equipment performance.
“You can infer a lot of information by vibration, especially on fixed assets,” explains Angus. “In one case at a poultry farm, we added sensors along the chain. The vibration of that chain is fairly constant throughout, so if something happens, it’s evident immediately.”
The benefits of telemetry for plant and equipment maintenance
Telemetry offers significant advantages for plant maintenance.
Telematic sensors enable continuous data collection, allowing for the immediate detection of anomalies and potential issues. This approach ensures more precise asset maintenance management, reducing the risk of unexpected breakdowns.
Predictive maintenance schedules informed by real-time data help prevent equipment overuse and underuse, which can negatively impact machinery. By anticipating maintenance needs and addressing issues proactively, you can reduce unplanned downtimes and extend asset life cycles. Operational efficiency is the winner here.
This is not to mention the financial benefits of optimising maintenance schedules and resource allocation.
“The cost of repairing a piece of broken down equipment is a lot more than the cost of maintaining,” explains Angus. “If you can be timely and predict things before they happen, you can save a lot of money.”
Angus adds that while maintenance personnel often know the machines intimately, telemetry brings science and data to the table like never before.
“You can’t replace knowledge and experience,” he says. “But telemetry can help. When you combine that experience with data from telemetry, you start predicting a lot more faults.”
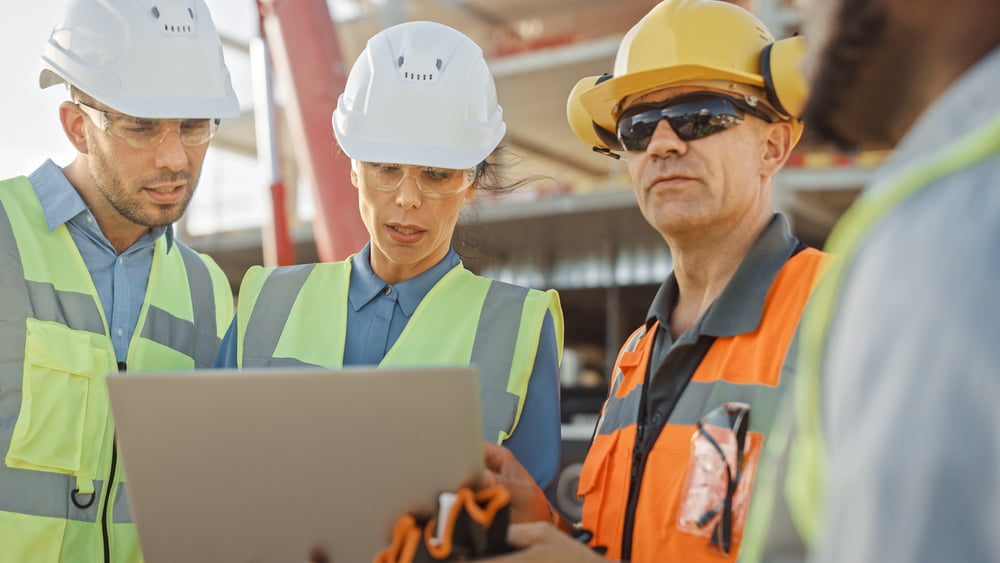
Adequate training, clear goals, continuous performance monitoring, and stakeholder involvement are key for successful asset maintenance management
Integrating telemetry with existing asset maintenance management
Angus admits that integrating telemetry with existing maintenance management systems and schedules isn’t straightforward. But there are big benefits if you have the right building blocks.
“None of the maintenance management systems out there today have been built to react to real-time information,” he explains. “The Perspio™ servicing module we’ve built helps to streamline that.”
The integration process starts with a thorough understanding of your current equipment and the parameters to monitor, such as engine hours or vibration. This gives you insight into what data to collect when installing telematic devices.
Angus advocates for a stepped approach, starting with basic tracking and then gradually incorporating predictive maintenance. It’s not as simple as installing sensors and changing systems overnight. Your maintenance team needs adequate training, clear goals, continuous performance monitoring and involvement from all stakeholders.
Embrace the potential of telemetry for plant maintenance
Telemetry in plant maintenance has the power to boost operational efficiency and reduce maintenance costs through opportunities for proactive maintenance and rapid identification of issues.
At Inauro, we start by understanding your unique operations and then tailor a solution to fit. Contact us to learn more about how the Perspio™ platform automates workflows for telemetry, ensuring optimal performance.